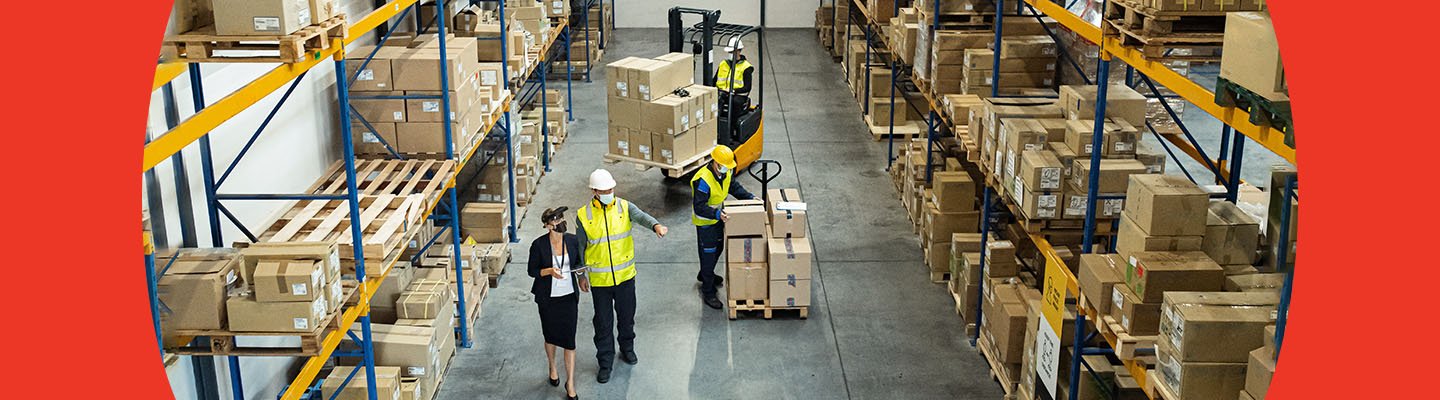
Industry Basics
13 December 2022 • 8 min read
Milk Run in logistics
Download Full Blog
Milk run keeps manufacturing activities moving throughout the shop floor, significantly reducing downtime.
The milk run has evolved over time to better integrate the logistical chain through planned routes. During large batch deliveries, this technique allowed for a reduction in the number of trucks while still maximising demand and the number of trips.
A Milk Run is a logistics delivery technique that guarantees that various deliveries from multiple vendors may be handled with optimal capacity utilisation and minimal expenditures. The term "Milk Run" refers to the process by which vehicles pick up milk from various suppliers and transfer it to a central location for processing. This method is how dairy cooperatives get their daily supply of milk.
A milk run makes sure that the shortest possible distance is covered and that the highest amount of demand is loaded into the truck or delivery vehicle to meet both the demand requirement and the need for efficient transportation at the lowest possible cost.

Importance of Milk Run
The milk run method is important as it encourages a process that is more effective and less expensive. Instead of each supplier or vendor sending several deliveries to a single point of demand, a single delivery vehicle travels to multiple sites to pick up the items. This guarantees cheaper costs and full vehicle use. It circles back around.
In lean and agile firms where reducing costs is essential, the milk run has become a significant concept. It makes sure that material delivery occurs at the most advantageous periods and is closely related to just in time.
Milk Run and Material Handling
Many lean manufacturing firms now frequently use the milk run approach within their operations. The lean philosophy places a strong emphasis on streamlining every step of manufacturing, including transportation and material handling. Simply said, the milk run method enables more frequent deliveries of materials and supplies to several assembly areas or areas of your business that require restocking. This frequently lowers the levels of overstocking or the need to manually request more materials.
Different components of the machinery are made in various areas of the facility. The assembly is done by a different team. The assembly division could receive finished items from each fabrication department. Sending a driver to each sector to load and carry all the pieces to the assembly location would likely be more effective, though. In this case, one driver replaces several, allowing each department's employees to focus on fabrication.

Adopting Milk Run in Supply Chain
The most typical configuration of this set-up involves operators and material handlers following predetermined standard delivery routes all throughout the building. These supplies are typically made to portions of the facility that are on the assembly line and are always in need of replenishment. For maximum efficiency throughout the shift, these delivery routes are typically timed out, allowing the assemblers to continue working in accordance with production schedules.
Before you get it right, adopting milk run may require a lot of testing, experimentation, and patience. One of the most important aspects of how you would need to set up your milk run routes is the layout of your facility or factory. The length of the route and the separation between the storage area and the various assembly locations all have a significant impact on how effective and efficient the route is.
It's simplest to describe the procedure using an example. Let's imagine that numerous growers from a single area provide wheat to a mill that produces flour. Every day, a delivery vehicle from each farm could deliver a load of grain to the mill.

Example of Milk Run
An automobile company can offer a good example of a milk run in logistics. Cars require numerous suppliers to deliver individual components. One truck may be dispatched by the manufacturer on a regular basis to make a milk run. That truck may make a circuit of pickups to collect the materials required for car assembly, such as steel, rubber, plastics, and aluminium.
The best method for this to happen is for the suppliers to be strategically placed geographically close to the manufacturing site and to one another. The milk run concept in logistics is related with just-in-time delivery requirements in addition to this advantage of combined pickup and delivery. The runs are planned at intervals to prevent downtime and to prevent overstocking supplies at the manufacturing site.
To be most effective, this technique probably needs to be improved over time. Along with explicit cost-sharing and scheduling agreements, it also needs support from all linked suppliers.
An efficient milk run in logistics therefore becomes routine, with loaders at each supplier arranging loads for pickup on time, the driver's journey time being planned, and receiving staff at the factory or other facility prepared for delivery at the predetermined time. This provides better operational certainty for loaders and receivers, as well as the opportunity to allocate resources only, when necessary, rather than continuously.
Optimizing both internal and external supply chains can be done in several innovative ways, such as a milk run. Cogoport can provide you services to help you manage your supply chain. Share your logistics requirements with us, and we will get in touch with you to talk about solutions.
Back to blog page
Schedule a personalized 1:1
Step into the future of freight forwarding with Cogoport. Experience a demo tailored to revolutionize your logistics, offering:
- Innovative Solutions: Peek into cutting-edge features redefining freight management.
- Expert Guidance: Direct insights from our seasoned pros, tailored to your business needs.
- Real Answers: Interactive session to address your unique challenges.
Blog comments